Batch digesters are a critical component of the pulping process and subjected to extreme conditions. Vapour flashing and accelerated material mass results in shock waves greater than 10,000 psi. These intense shockwaves can shake the batch digester loose causing damage to piping and valves.
Many pulp mills have endured years of costly interruptions to production due to the poor reliability of blowdown valves, blow lines and associated gaskets. To help pulp mill operators improve reliability in batch digester blowdown operations, Stainless Valve Company specifically designed The Big BlowTM valve to handle intense shock waves, system vibration and sudden changes in temperature.
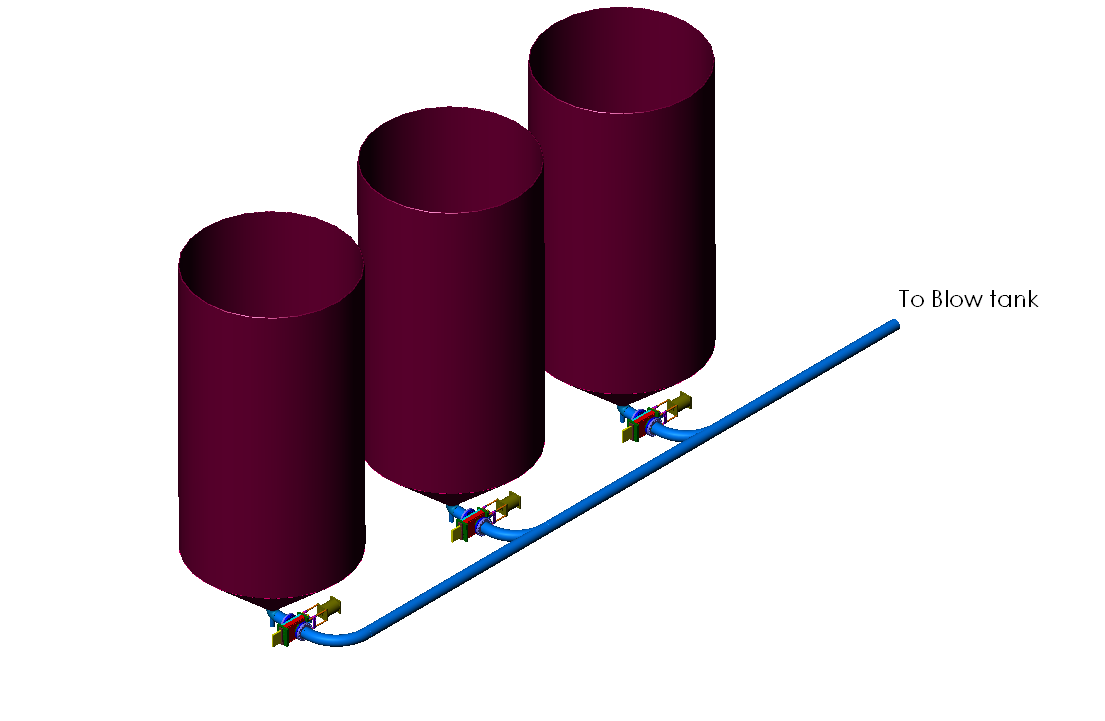
Photo Credit: Stainless Valve Company
Batch Digester Blowdown Operations
North American Pulp Mills are typically designed with common blow lines that lead to blow tanks, known as a common header system, in lieu of individual blow lines from each digester to a blow tank. While a common header system is more cost effective, there are indeed challenges.
Shock loads generated when residual liquor in blow lines flash off as an adjacent digester is blown often result in the failure of associated valves and piping. The shock loads can crack blowdown valve seats, which in turn accentuates valve leakage that results in subsequent shock loads.
Leaking blow valves not only change pulp property and result in loss of energy, but also leave cold liquid in the line. When any of the digesters blows, the hot pulp and black liquor encounters residual cold liquid from previous blows in the common header. This cold liquid flashes, causing shock waves. While shock waves cannot be completely eliminated in a common header system, there are measures which can be taken to minimize the negative effects of shock waves on blowdown valves.
Utilizing Ball Valves vs. Big BlowTM Valves in Blowdown Operations
While metal seated ball valves are often used as blow valves, they may not be the ideal solution for plants looking for performance and reliability. At the start of a blow, a ball valve is in the partially open position. The flow going through the ball valve hits the seats directly, which can cause premature damage. During operation, the flow of material is redirected twice as it passes through the ball valve. Again, reaction forces are generated, resulting in shock loads.
With the Big BlowTM valve, the seat is always protected as it is away from the flow direction. In addition, there is no redirection of the flow, which makes the blow faster, much quieter, and less violent. There is no opportunity for material to build up behind the blade as it may behind the ball.
Metal seated ball valves are also prone to mechanical impact in blowdown operations. Any hard object that comes in contact with the seats or balls with sufficient load can indent the ductile ball substrate. The ball coating is generally hard and brittle and will crack and delaminate once indentation has occurred (see pic 2).
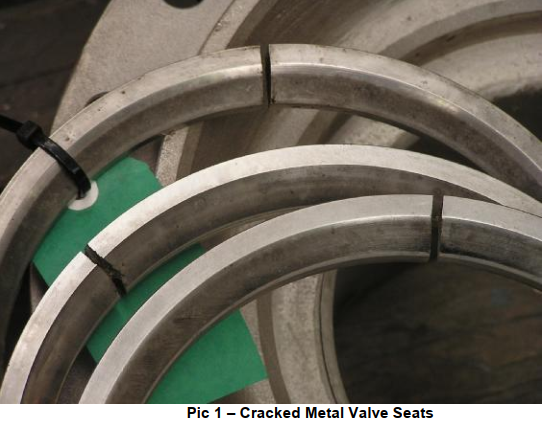

Photo Credit: Stainless Valve Company
Pulp mill operators seeking to improve the reliability of their batch digester blowdown operations may consider utilizing a blowdown valve specifically developed for batch digesters. Developed by Stainless Valve Company in 1968, the Big BlowTM valve is engineered with this critical and severe service application as a top priority.
The Big BlowTM valve is proven to perform despite abrasion, corrosion, shock waves, system vibration and sudden changes in temperature. The following design features of the Big BlowTM valve can help resolve operational challenges faced by pulp mill operators.

The Big Blow Valve TM
- Thick side plates and blades (97% of the valve body is solid plate material) support the glands on either side of the valve, providing extra stability during shock waves.
- The valve is sealed on both ends by packing boxes to prevent material from escaping through the body and the sealing material utilized ensures that no leakage from the valve occurs despite heavy shock waves and slurry material in the line.
- Reinforced and modified PTFE seats maintain their position despite shock waves; preloaded seats made of 25% glass filled PTFE allow for a tight seal, guarantee no leakage, and maintain a tight shutoff regardless of pressure differential.
- Blade guides are engineered to handle abrasive and erosive media along with vapour flashing and mechanical shock waves.
- Minimal maintenance is required with refurbishments spanning 3 to 7 years, depending on the piping system, frequency of cycling and process conditions.
- The valve can serve as a drop-in replacement for a standard ball valve with no piping rework or additional support required.
- The opening of a Big BlowTM valve can be controlled from approximately 10 to 60 seconds. This is advantageous as the fast opening of blow valves can result in the pressure in the digester expanding and sudden decompression can cause the digester and piping to shake.
Our Expertise
In collaboration with our partners, Armour Valve can provide custom-engineered valve solutions to handle even the most challenging applications. Our knowledgeable team members are here to help you select the right equipment whether you are looking for solutions to handle black liquor, slurry and scaling applications or to improve the reliability of your batch digester blowdown operations. Connect with us today.