Pulp mills using the kraft process to convert wood into wood pulp invariably must deal with black liquor. This by-product of the digester is a combination of lignin, hemicellulose, spent chemicals, and water. Typically, the liquor must be pumped to an evaporation plant where is it is concentrated, and then burnt to produce energy and recover the cooking chemicals. However, during this process, black liquor puts unusual demands on valves. It is thick, sticky, and (particularly when leaving the evaporation plant to be combusted) has a high solid content. Somas ball segment valves are specifically designed to handle black liquor at each stage of the evaporation process.
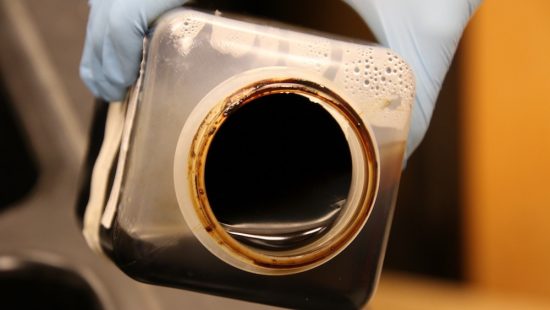
Photo Credit: FPInnovations
Efficiency in the Evaporation Plant
For black liquor to be combustible, it must reach at least 60% dryness. As the liquor leaves the washing station, it is made up of about 15% dry substances, so it must be pumped into an evaporation plant to be concentrated.
Ideally, you’ll want to evaporate black liquor in the most cost-effective way. Connecting several evaporators in a series and running the liquor through them in sequence has several advantages, as each evaporator handles a portion of the temperature change. About 0.2 tonne live steam is sufficient to evaporate 1 tonne of water from the black liquor; the steam from one evaporator can be used in the next to reduce how much steam you need to produce.
Valves for Evaporation of Black Liquor
So, which control valve should you use during the evaporation process? In the early stages of the process, Somas eccentric butterfly valves are a wise choice because they can handle the black liquor until the substance exceeds 45-50% solids. Once the liquor is evaporated beyond this point, a better choice is Somas standard Ball Segment valve KVTW/KVTF, which can handle the higher solid percentages and additional physical demands of the partly evaporated substance.
Valves for Black Liquor After Evaporation
Which valves can handle the stresses of bringing the concentrated black liquor to the recovery boiler? At this point, the solution is heavy and may have up to 70% solids, combined with salt cake and sulfur. This is an exceptionally clingy and thick substance that presents challenges for any valve type. Common failures include build-up around shafts and seats which cause valves to stick or leak.
The Somas HVV ball segment valve and the SKV ball valve, configured for black liquor applications, are ideal at this stage of the process. In this configuration, a PTFE shaft seal prevents the black liquor from entering the bearing area. A shaft bearing ensures smooth movement of the shaft during operation, and further protects the shaft in the event that any liquor does enter this area of the valve.
There is also a risk that the media will enter behind the seats and block the operation of the valve. To account for this, the design features locked in seats. The Somas HVV valve applies to control applications and the SKV ball valve is the valve of choice for on/off isolation applications. Further, valves that are in contact with black liquor should be equipped with heat tracing. Keeping the valve body warm will prevent the black liquor from solidifying and making the valve inoperable during the start up of an unplanned shutdown.
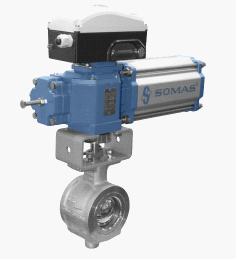
Importance of the Recovery Boiler
After it has been evaporated, black liquor is burned in a recovery boiler, which serves three key functions:
- Eliminates black liquor: The recovery boiler destroys the organic matter in black liquor and is an environmentally-sound method of dealing with this by-product.
- Generates steam: The recovery boiler creates all of the steam needed in a kraft pulp mill. The steam turbine produces electrical power for the mill.
- Creates chemical reactions: The boiler also produces sodium carbonate (Na2CO3) and sodium sulphide (Na2S).
In the recovery boiler’s lower furnace, the final sulphide compound is created from the various organic and inorganic compounds in the black liquor. This compound is an active kraft pulping agent. The measure of success of the chemical recovery process is the reduction efficiency.
Our Expertise
Armour Valve’s knowledgeable team is here to help you select the right equipment to handle even the most challenging applications. Whether you’re handling black liquor or other thick, sticky substances, you can contact our team to discuss which valves can safely stand up to the demands of your application most cost-effectively. Connect with us today.