Problem:
One major Alberta SAGD operator drew its process water from a deep source well (500-600 meters) containing brackish water. The water had a high chloride content and was contaminated by solid particles finer than beach sand. It was not possible to detect these water quality issues prior to drilling the well.
Maintenance personnel detected repeated jamming of the automatic recirculation valves (ARVs) protecting three centrifugal pumps that were used to introduce make-up water into the process. In addition, the valves’ springs would become brittle and disintegrate.
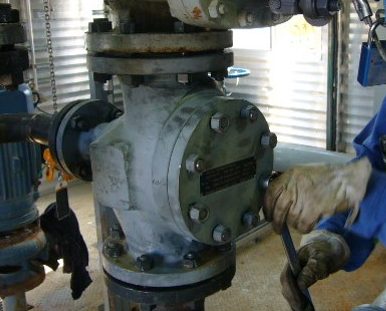
The HORA Automatic recirculation valve is in-line repairable
Repairing the existing valves took two days from start to finish, repeated as often as every 3 weeks for each of the three automatic recirculation valves.
The jamming was caused by the build-up of sand contaminants, while the cause of spring failure was undetermined. Either issue would result in valve failure. Maintenance personnel also observed pitting of the valve body.
Each valve would fail as often as every 3 weeks. In order to service a valve, maintenance personnel would use a truck-mounted picker to remove the valve from service and transport it to a maintenance shop. There, it was opened, cleaned, and, if necessary, the springs were replaced. The serviced valve was then returned to the unit, where it was reinstalled.
Servicing did not result in production downtime, as the two other pumps could handle the workload; however, it was a costly undertaking involving approximately one full worker day per valve. The cost of the replacement springs was approximately $1,000 each. The entire process took two days from start to finish, repeated as often as every 3 weeks for each of the three valves.
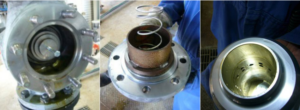
HORA: Pump Recirculation Valve After 2 Year Trial Period
Solution:
Unsatisfied with the frequent failure and costly servicing of their ARVs, plant personnel actively sought an alternative and were introduced to the HORA ARV.
HORA’s top entry design enabled the valves to be opened and cleaned without removal from the line. Parts could be replaced in minutes by simply removing the bolted cover, removing the check valve insert assembly, installing replacement parts, and replacing the cover.
Whereas the original valve was only available in one material, the spring and trim materials on the HORA ARV were customizable. HORA also offered 75% faster lead times and a significantly lower unit cost.
Impact:
Over a two-year trial period, maintenance personnel observed no pitting of body surfaces or disintegration of check valve insert springs on the HORA ARVs (see photos below).
The valves proved themselves to be durable and offered considerable maintenance cost and time savings. HORA is exploring modifications to further improve valve performance in this challenging service.
Not only did the HORA ARV lower capital and maintenance costs for this major SAGD operator; it can be easily inspected and serviced, and its body castings reduce delivery times and costs. For these reasons, it has become the operator’s preferred ARV valve for pump protection.
Criteria | Original valve | HORA ARV |
---|---|---|
Worker-hours | 19 hrs | <1hr |
Total Repair time | 2 days | <1hr |
Replacement spring | $1000 | N/A |
AVG time between repairs | 3 wks | |
Lead time (wks) | 22-26 | 16-18 |
Custom material | No | Yes |