Problem:
A well-known brand of choke valve was in use on a SAGD high-pressure steam separator blowdown line. These valves would operate for a few days to a week before they would start to leak. The valves were leaking due to erosion incurred when blowing down the dissolved solids and organics the were present in the media.
As a result of the leakage, the internal parts of the valve became worn and the plant’s maintenance team had to replace the valves every four months. Whenever the valves needed servicing, the plant would be forced to undergo a costly shutdown.
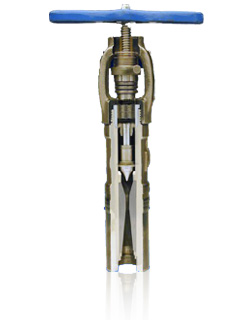
Solution:
An operation shift supervisor who had previous experience with Conval products recommended them to the plant reliability engineer as a possible solution. Armour Valve and Conval analyzed the conditions and proposed a Conval Clampseal throttling valve for the application
The Conval Throttling Valve was proposed due to its modular design which allows it to be serviced quickly and easily. Service can be performed in-line by disassembling the valve top work and replacing the seat and stem assembly as needed.
Servicing instructions and hands-on training were provided to maintenance personnel by factory-trained technicians. The in-line repairable valves would provide the plant with significant cost savings through reduced downtime, labour, and maintenance expenses.
Conval Clampseal throttling valves were installed on a trial basis.
Impact:
Unlike the choke valves that required frequent replacement, Conval Clampseal Throttling valves are inspected and serviced only every two years as part of the plant’s routine preventive maintenance program. This saves the plant a considerable amount of lost production time, service time, and money; amounting to an estimated $700-800K per year.
After this successful trial, the plant installed twenty (20) Conval Clampseal Throttling valves on various boiler blowdown lines on three steam generators.
The Conval throttling valve remains the valve of choice on the blowdown evaporator system at this major SAGD facility and plant personnel continue to look to Armour Valve for solutions to their valve challenges in various applications.